一、焊接是一种常见的钢结构连接方式,其优点在于施工简便、节省材料、密封性好等。在选择焊接连接时,应充分考虑焊缝的位置、数量和尺寸,以保证焊接的质量和稳定性。以下部分为焊接连接在相关规范中要求。
(一)《钢结构工程施工质量验收规范》(GB50205-2020) 第8.2.2条:焊接H型钢的翼缘板拼接缝和腹板拼接缝的间距,不宜小于200mm。翼缘板拼接长度不应上小于600mm;腹板拼接宽度不应小于300mm,长度不应小于600mm。第8.2.3条:箱型构件的侧板拼接长度不应小于600mm,相邻两侧板拼接缝的间距不宜小于200mm,侧板在宽度方向不宜拼接,当宽度超过2400mm确需拼接时,.小拼接宽度不宜小于板宽的1/4。第8.2.4条:设计无特殊要求时,用于次要构件的热轧型钢可采用直口全熔透焊接拼接,其拼接长度不应小于600mm。第8.2.5条:钢管接长时每个节间宜为一个接头,.短接长长度应符合下列规定:1.当钢管直径d≤500mm时,不应小于500mm;2.当钢管直径500mm<d≤1000mm时,不应小于直径d;3.当钢管直径>1000mm时,不应小于1000mm;4.当钢管采用卷制方式加工成型时,可有若干个接头,但.短接长长度应符合第1~3款的要求。
第8.2.6条:钢管接长时,相邻管节或管段的纵向焊缝应错开,错开的.小距离(沿弧长方向)不应小于钢管壁厚的5倍,且不应小于200mm。
(二)《钢结构设计标准》(GB50017-2017)
第11.1.6条:焊缝质量等级应根据钢结构的重要性、荷载特性、焊缝形式、工作环境以及应力状态等情况,按下列原则选用:1.在承受动荷载且需要进行疲劳验算的构件中,凡要求与母材等强连接的焊缝应焊透,其质量等级应符合下列规定:1)作用力垂直于焊缝长度方向的横向对接焊缝或T形对接与角接组合焊缝,受拉时应为一级,受压时不应低于二级。
2)作用力平行与焊缝长度方向的纵向对接焊缝不应低于二级。
3)铁路、公路桥的横梁接头板与弦杆角焊缝应为一级,桥面板与弦杆角焊缝、桥面板与U形肋角焊缝不应低于二级。4)重级工作制(A6~A8)和起重量Q≥50t的中级工作制(A4、A5)吊车梁的腹板与上翼缘板之间以及吊车桁架上弦杆与节点板之间的T形接头焊缝应焊透,焊缝形式宜为对接与角接的组合焊缝,其质量等级不应低于二级。
2.不需要疲劳验算的构件中,凡要求与母材等强的对接焊缝宜焊透,其质量等级受拉时不应低于二级,受压时不宜低于二级。
3.部分焊透的对接焊缝,采用角焊缝或部分熔透的对接与角接组合焊缝的T形接头,以及搭接连接角焊缝,其质量等级应符合下列规定:1)直接承受动荷载且需要疲劳验算的结构和吊车起重量等于或大于50t的中级工作制的吊车梁以及梁柱、牛腿等重要节点不应低于二级。
2)其他结构可为三级。
(三)《钢结构设计标准》(GB50017-2017)
第11.3.1条:受力和构造焊缝可采用对接焊缝、角接焊缝、对接与角 接组合焊缝、塞焊焊缝、槽焊焊缝,重要连接或有等强要求的对 接焊缝应为熔透焊缝,较厚板件或无需焊透时可采用部分熔透焊缝。第11.3.3 不同厚度和宽度的材料对接时,应作平缓过渡,其连接处坡度值不宜大于1 : 25
第11.3.4条:承受动荷载时,塞焊、槽焊、角焊、对接连接应符合下列规定:1.承受动荷载不需要进行疲劳验算的构件,采用塞焊、槽焊时,孔或槽的边缘到构件边缘在垂直于应力方向上的问距不应小于此构件厚度的5倍,且不应小于孔或槽宽度的2倍;构件端部搭接连接的纵向角焊缝长度不应小于两侧焊缝间的垂直间距a,且在无塞焊、槽焊等其他措施时,间距不应大于较薄件厚 16 倍。
2.不得采用焊脚尺寸小于5mm的角焊缝。
3.严禁采用断续坡口焊缝和断续角焊缝。
4.对接与角接组合焊缝和形连接的全焊透坡口焊缝应采 用角焊缝加强,加强焊脚尺寸不应大于连接部位较薄件厚度的 1/2 ,但.大值不得超过lOmm。5.承受动荷载需经疲劳验算的连接,当拉应力与焊缝轴线垂直时,严禁采用部分焊透对接焊缝。
6.除横焊位置以外,不宜采用L形和J形坡口。
7.不同板厚的对接连接承受动载时,应按本标准第 11. 3. 3 条的规定做成平缓过渡。
第11.3.5条:角焊缝的尺寸应符合下列规定:
1.角焊缝的.小计算长度应为其焊脚尺hf的8倍,且不应小 40mm;焊缝计算长度应为扣除引弧、收弧长度后的焊缝长度。
2.断续角焊缝焊段的.小长度不应小于.小计算长度。
3.角焊缝.小焊脚尺寸宜按表 11.3.5 取值,承受动荷载时角焊缝焊脚尺寸不宜小于 5mm。
4.被焊构件中较薄板厚度不小于25mm时,宜采用开局部坡口的角焊缝。
5.采用角焊缝焊接连接,不宜将厚板焊接到较薄板上。
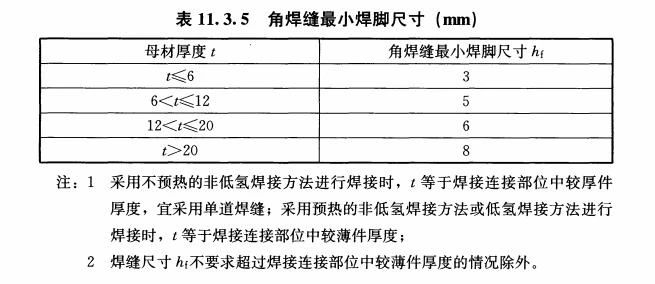
第11.3.6条:搭接连接角焊缝的尺寸及布置应符合下列规定:
1.传递轴向力的部件,其搭接连接.小搭接长度应为较薄件厚度的5倍,且不应小于 25mm (图 11.3.6-1 )并应施焊纵向或横向双角焊缝。
2.只采用纵向角焊缝连接型钢杆件端部时,型钢杆件的宽度不应大于200mm ,当宽度大于200mm时,应加横向角焊缝或中间塞焊;型钢杆件每一侧纵向角焊缝的长度不应小于型钢杆件的宽度。3.型钢杆件搭接连接采用围焊时,在转角处应连续施焊。杆件端部搭接角焊缝作绕焊时,绕焊长度不应小于焊脚尺寸的2倍,并应连续施焊。4.搭接焊缝沿母材棱边的.大焊脚尺寸,当板厚不大于6mm 时,应为母材厚度,当板厚大于6mm 时,应为母材厚度减 lmm ~2mm。
5.用搭接焊缝传递荷载的套管连接可只焊一条角焊缝,其管材搭接长度不应小于5(t1+t2),且不应小于25mm 。搭接焊缝焊脚尺寸应符合设计要求。第11.3.7条:塞焊和槽焊焊缝的尺寸、间距、焊缝高度应符合下列规定:1.塞焊和槽焊的有效面积应为贴合面上圆孔或长槽孔的标称面积。2.塞焊焊缝的.小中心间隔应为孔径的4倍,槽焊焊缝的纵向.小间距应为槽孔长度的2倍,垂直于槽孔长度方向的两排槽孔的.小间距应为槽孔宽度的4倍。
3.塞焊孔的.小直径不得小于开孔板厚度加8mm ,.大直径应为.小直径加 3mm 和开孔件厚度的 2.25倍两值中较大者。槽孔长度不应超过开孔件厚度的 10 倍,.小及.大槽宽规定应与塞焊孔的.小及.大孔径规定相同。
1)当母材厚度不大于16mm 时,应与母材厚度相同。2)当母材厚度大于16mm 时,不应小于母材厚度的一半 16mm两值中较大者。
二、螺栓连接是一种简便的钢结构连接方式,其优点在于施工方便、安装快捷、可拆卸等。在选择螺栓连接时,应充分考虑螺栓的规格、数量和排列方式,以保证连接的稳定性和安全性。以下部分为螺栓连接在《钢结构设计标准》(GB50017-2017)中的要求。
第11.3.8条:在次要构件或次要焊接连接中,可采用断续角焊缝。断续角焊缝焊段的长度不得小于l0h£或50mm ,其净距不应大于15t(对受压构件)或30t(对受拉构件),t为较薄焊件厚度。腐蚀环境中不宜采用断续角焊缝。第11.5.1条:螺栓孔的孔径与孔型应符合下列规定:1.B级普通螺栓的孔径比较螺栓公称直径大0.2mm~ 0.5mm,C级普通螺栓的孔径较螺栓公称直径大l.Omm~ 1.5mm。2.高强度螺栓承压型连接采用标准圆孔时,其孔径。可按表11.5.1采用。3.高强度螺栓摩擦型连接可采用标准孔、大圆孔和槽孔,孔型尺寸可按表 11.5.1采用;采用扩大孔连接时,同一连接面只能在盖板和芯板其中之一的板上采用大圆孔或槽孔,其余仍采用标准孔。
4.高强度螺栓摩擦型连接盖板按大圆孔、槽孔制孔时,应增大垫圈厚度或采用连续型垫板,其孔径与标准垫圈相同,对M24及以下的螺栓,厚度不宜小于8mm ;对 M24 以上的螺栓,厚度不宜小于lOmm。
第11.5.2条:螺栓(铆钉)连接宜采用紧凑布置,其连接中心宜与被连接构件截面的重心相一致。螺栓或例钉的间距、边距和端距容许值应符合表 11.5.2的规定。
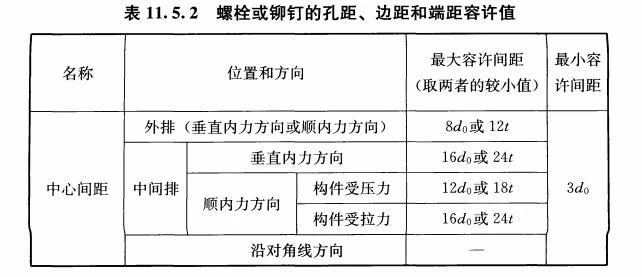
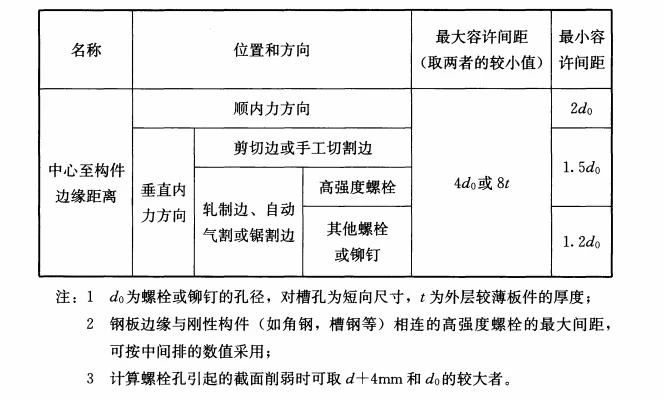
第11.5.3条:直接承受动力荷载构件的螺栓连接应符合下列规定:2.普通螺栓受拉连接应采用双螺帽或其他能防止螺帽松动的有效措施。第11.5.4 高强度螺栓连接设计应符合下列规定:1.本章的高强度螺栓连接均应按本标准表 11.4.2-2 施加预拉力。2.采用承压型连接时,连接处构件接触面应清除油污及浮锈,仅承受拉力的高强度螺栓连接,不要求对接触面进行抗滑移处理。3.高强度螺栓承压型连接不应用于直接承受动力荷载的结构,抗剪承压型连接在正常使用极限状态下应符合摩擦型连接的设计要求。4 当高强度螺栓连接的环境温度为100 ℃~ 150 ℃时,其承载力应降低10%。第11.5.5条:当型钢构件拼接采用高强度螺栓连接时,其拼接件宜采用钢板。2.螺栓连接或拼接节点中,每一杆件一端的..性的螺栓数不宜少于2个;对组合构件的缀条,其端部连接可采用1个螺栓。3.沿杆轴方向受拉的螺栓连接中的端板(法兰板),宜设置加劲肋。
总结:钢结构的连接方式是钢结构设计中的重要环节,选择合适的连接方式对于保证钢结构的可靠性、经济性和施工便利性具有至关重要的影响。在选择连接方式时,应充分考虑施工条件、材料成本、连接强度和稳定性等因素。同时,还应注意加强焊接、铆钉和螺栓连接施工质量的控制,确保钢结构的整体安全性和稳定性。未来,随着科技的不断发展和新材料的出现,钢结构的连接方式将会不断得到优化和改进。